新能源锂电池焊接的现状与挑战
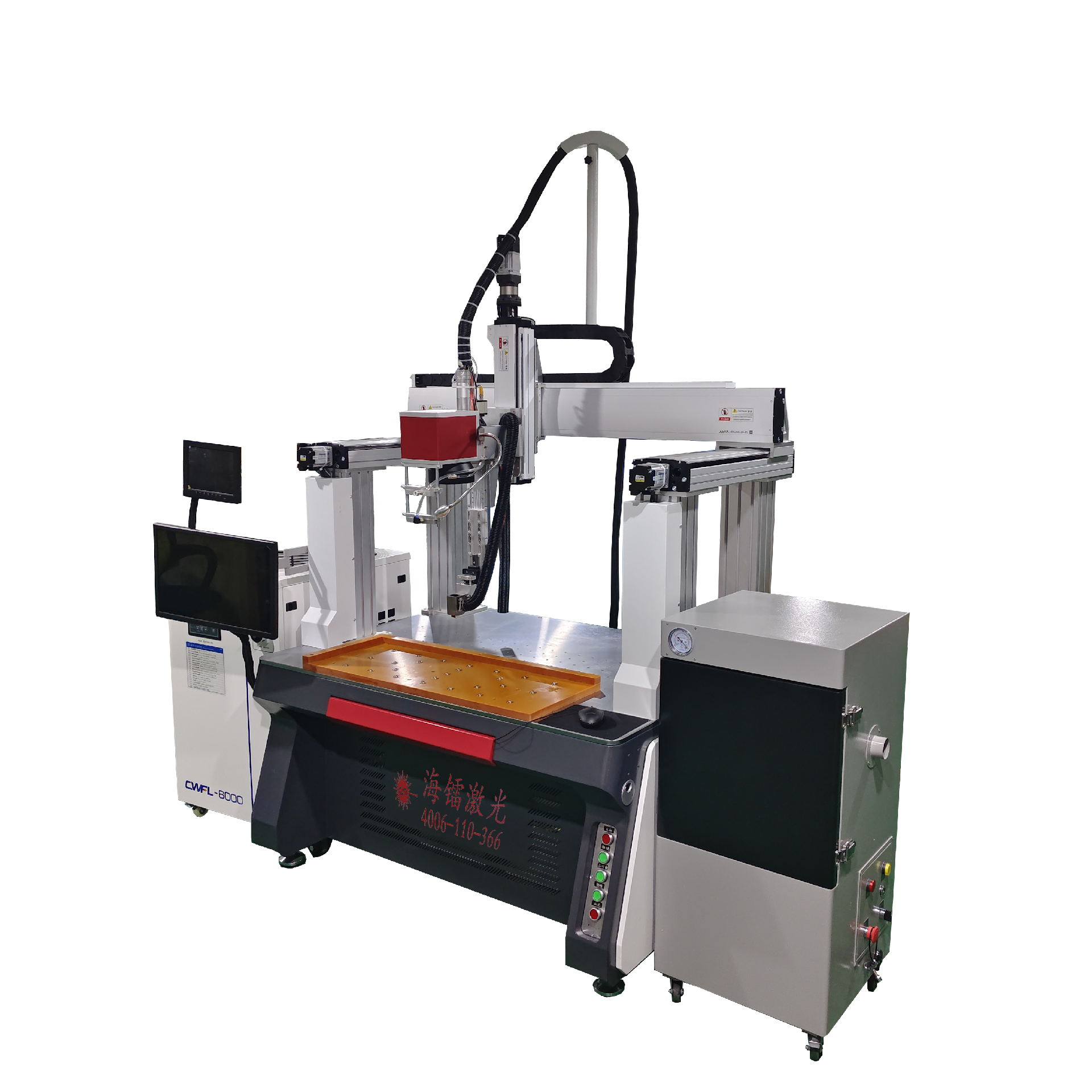
在 “双碳” 目标引领下,新能源产业正以前所未有的速度蓬勃发展,作为其核心储能单元的锂电池,已然成为推动这一变革的关键力量。从电动汽车的迅猛崛起,到储能系统在智能电网中的广泛应用,锂电池凭借其高能量密度、长循环寿命等优势,成为新能源领域不可或缺的一环。据高工产研锂电研究所(GGII)数据显示,2023 年全球锂电池出货量达 957.7GWh,同比增长 35.8% ,预计到 2025 年,这一数字将突破 1500GWh。如此庞大的市场需求,对锂电池的生产制造工艺提出了严苛挑战,其中焊接工艺的重要性尤为凸显。
焊接作为锂电池制造过程中的关键环节,直接关乎电池的性能、安全性以及使用寿命。在锂电池的生产流程中,从电芯极耳与汇流排的连接,到电池外壳的密封焊接,每一个焊点的质量都如同链条上的关键一环,决定着整个电池系统的可靠性。一个微小的焊接缺陷,都可能导致电池内阻增大、容量衰减,甚至在极端情况下引发短路、起火等安全事故,这对于新能源汽车、储能电站等应用场景而言,无疑是巨大的隐患。
当前,新能源锂电池焊接工艺面临着诸多难点。锂电池外壳多采用铝合金材料,铝合金对激光的反射率高达 60%-98%,这使得激光能量难以有效耦合到材料中,焊接难度大幅增加。焊接过程中,铝合金还容易产生气孔、热裂纹等缺陷。由于激光焊接冷却速度极快,氢气孔问题尤为突出,小孔塌陷也会导致孔洞产生;而铝合金典型的共晶型合金特性,使其在焊接时焊缝区易发生成分偏析,引发晶界熔化,在应力作用下形成热裂纹,降低焊接接头性能。
不同类型的锂电池,如方形、圆柱、软包电池,因其结构和材料的差异,对焊接工艺有着独特的要求。方形电池在组合焊接时,极柱或连接片若受污染,焊接时污染物分解易形成炸点,造成孔洞;极柱较薄或下方有塑料、陶瓷结构件时,容易焊穿,极柱较小时还易焊偏,导致塑料烧损形成爆点。圆柱电芯焊接主要用于正极,负极部位壳体薄,极易焊穿。软包极耳焊接则对焊接工装要求较高,必须将极耳压牢,保证焊接间隙,才能确保焊接质量。
龙门式振镜激光焊接机的工作原理与独特优势
面对新能源锂电池焊接的复杂现状,龙门式振镜激光焊接机脱颖而出,凭借其先进的工作原理和显著优势,成为解决焊接难题的理想方案。
(一)工作原理揭秘
龙门式振镜激光焊接机的工作过程犹如一场精密的光学与机械协同的 “舞蹈”。首先,由高性能的激光发生器产生高能量密度的激光束,这是整个焊接过程的 “能量源泉”。常见的光纤激光器以其卓越的稳定性和高效率,为焊接提供持续且强大的能量输出 。产生的激光束通过光纤这一 “能量传输通道”,被精确地传导至振镜扫描系统。
振镜扫描系统堪称设备的 “灵动之手”,它主要由两个相互垂直的反射镜组成,分别负责 X 轴和 Y 轴方向的激光束偏转。在高速马达的驱动下,这两个反射镜能够按照预设的程序,以极高的速度和精度进行摆动,实现激光束在工件表面的快速扫描和定位。想象一下,激光束就像是一支由振镜操控的 “画笔”,能够在电池的极耳、汇流排等部件上精准地 “绘制” 出焊缝。
在激光束到达工件表面之前,还需经过聚焦系统的 “聚焦强化”。聚焦透镜将激光束汇聚成极小的光斑,大幅提高了能量密度,犹如将分散的阳光通过放大镜聚焦后产生高温一样,使激光能量能够高度集中地作用于焊接部位,瞬间熔化材料形成熔池。随着激光束在振镜的控制下不断移动,熔池也随之移动,当激光束离开后,熔池迅速冷却固化,最终形成牢固、精密的焊缝,将电池部件紧密连接在一起。
(二)优势全方位剖析
焊接精度与质量:龙门式振镜激光焊接机以其卓越的光斑控制能力,实现了高精密焊接。其光斑细如发丝,光束分布均匀,能够在微小的电池部件上进行精确焊接。焊点大小可根据焊接需求进行灵活调整,无论是极耳与汇流排的细微连接,还是电池外壳的密封焊接,都能轻松应对,确保焊接质量达到行业顶尖水平。这不仅有效提升了电池的电气性能,还大大降低了因焊接缺陷导致的电池失效风险,为锂电池的长寿命、高安全性提供了有力保障。
效率与稳定性:设备采用的光纤连续焊接光源,搭配稳定可靠的伺服系统,如同为焊接过程注入了 “稳定器” 和 “加速器”。光纤连续焊接光源能够提供持续、稳定的激光输出,避免了传统焊接方式中能量波动对焊接质量的影响。伺服系统则以其快速响应和精准控制的特点,确保激光束能够按照预设轨迹高速、稳定地移动,大大提高了焊接效率。在大规模锂电池生产中,这种高稳定性和高效率的焊接方式,能够显著缩短生产周期,提高产能,为企业带来巨大的经济效益。
成本与维护:从长期使用成本来看,龙门式振镜激光焊接机具有无可比拟的优势。其电能损耗低,相比传统焊接设备,能够为企业节省大量的电费支出。设备结构紧凑,占地面积小,在寸土寸金的生产车间中,有效节省了空间资源。而且,设备的日常维护成本低,激光器理论寿命可达 10 万小时,减少了频繁更换设备带来的高昂成本和停机时间,为企业的持续生产提供了坚实保障。
操作便捷性:考虑到生产现场操作人员的需求,龙门式振镜激光焊接机配备了全中文操作界面,简洁直观,易于上手。专业的焊接软件提供了丰富的参数设置和图形编辑功能,操作人员只需通过简单的鼠标点击和参数输入,就能轻松完成复杂的焊接任务。即使是初次接触设备的新手,也能在短时间内熟练掌握操作技巧,大大提高了生产效率,降低了人力成本。
在新能源锂电池焊接中的具体应用场景
(一)电池极耳焊接
极耳作为锂电池电芯与外部电路连接的关键部件,其焊接质量直接影响电池的充放电性能和使用寿命。在动力电池的制造过程中,需要将电池极耳与极柱可靠地焊接在一起,在二次电池制作中,还需与铝制安全阀焊接。这不仅要求焊接能够保证极耳与极柱之间的电气连接稳定,承载大电流传输,还对焊缝的平滑美观有着严格要求,以避免因焊缝缺陷导致的局部电阻增大、发热甚至断裂等问题。
龙门式振镜激光焊接机在极耳焊接中展现出卓越的性能。凭借其高精度的光斑控制和灵活的扫描速度调节能力,能够精确地在极耳与极柱的接触部位形成高质量的焊点。对于不同材质的极耳,如正极常用的铝材质和负极的镍或铜镀镍材质,通过优化激光焊接参数,如功率、脉冲宽度、频率等,确保在焊接过程中既能实现良好的冶金结合,又能避免对极耳和极柱造成热损伤。在焊接铝极耳时,利用设备的高能量密度和快速焊接特性,有效减少铝合金焊接时的气孔和热裂纹等缺陷,保证焊缝的致密性和强度,实现了极耳与极柱之间可靠连接,且焊缝平滑美观,满足了锂电池对极耳焊接的高要求。
(二)电池壳体与盖板封口焊接
电池壳体与盖板的封口焊接是保证电池密封性和安全性的关键环节。目前,动力电池的壳体材料主要有铝合金和不锈钢,其中铝合金因具有重量轻、比强度高等优点而被广泛应用,常见的如 3003 铝合金 。然而,铝合金的高反射率和高导热性使其焊接成为一大挑战。
龙门式振镜激光焊接机针对铝合金焊接难点,采用了一系列先进技术。通过优化激光光束质量和光斑形状,提高了铝合金对激光能量的吸收率。在焊接过程中,精确控制激光功率和焊接速度,利用激光的高能量密度迅速熔化铝合金材料,形成稳定的 “小孔” 效应,实现高效焊接。与传统焊接方法相比,龙门式振镜激光焊接机在电池壳体与盖板封口焊接中具有显著优势。在效率方面,其高速的振镜扫描系统能够实现快速焊接,大大缩短了焊接时间,提高了生产效率。在密封性上,激光焊接形成的焊缝窄且连续,能够有效阻挡外界杂质和水分进入电池内部,确保电池在各种复杂环境下的稳定性和安全性。而传统焊接方法,如 TIG 焊或 MIG 焊,不仅焊接速度慢,热输入大导致电池壳体变形,还难以保证焊缝的密封性,容易引发电池内部短路等故障。
(三)电池模组及 pack 焊接
在动力电池模组及 pack 焊接中,需要实现多个单体电池之间的串并联连接,这就涉及到不同材质连接片的焊接。常见的连接片材质有铜和铝,由于铜和铝的物理性能差异较大,如熔点、热膨胀系数等,采用激光焊接时容易形成脆性金属间化合物,降低焊接接头的力学性能和导电性,无法满足电池模组及 pack 的使用要求。因此,除了铜铝连接通常采用超声波焊接外,铜和铜、铝和铝之间的焊接一般采用激光焊接。
龙门式振镜激光焊接机在应对铜、铝等不同材质连接片的焊接需求时,展现出强大的适应性。对于高反射率且导热快的铜、铝材料,通过提高激光器功率,增加激光能量输入,确保焊接过程中材料能够充分熔化。同时,利用设备的高精度定位和快速扫描功能,精确控制焊接位置和焊缝形状,避免因焊接偏差导致的连接不良。在解决铜铝焊接难题方面,虽然主要采用超声波焊接,但龙门式振镜激光焊接机在一些特殊工艺要求下,通过优化焊接参数和添加过渡层等方法,也能在一定程度上实现铜铝之间的可靠连接。在电池模组及 pack 的大规模生产中,龙门式振镜激光焊接机以其高效、稳定的焊接性能,满足了不同材质连接片的焊接需求,为提高电池模组及 pack 的生产质量和效率提供了有力支持。
实际案例见证实力
实践是检验真理的唯一标准,龙门式振镜激光焊接机在众多新能源锂电池制造企业中得到了广泛应用,并取得了显著成效。
某知名新能源汽车电池生产企业,在引入龙门式振镜激光焊接机之前,采用传统焊接工艺,生产效率较低,每小时只能完成 50 个电池模组的焊接。焊接质量也不稳定,焊缝存在气孔、裂纹等缺陷,导致产品合格率仅为 80%。这不仅增加了生产成本,还影响了企业的市场声誉。
在采用龙门式振镜激光焊接机后,生产效率得到了大幅提升。设备的高速振镜扫描系统和稳定的激光输出,使焊接速度大幅提高,每小时可完成 120 个电池模组的焊接,生产效率提升了 140%。焊接质量也得到了显著改善,焊缝均匀、致密,几乎无气孔、裂纹等缺陷,产品合格率提高到了 95% 以上。这不仅降低了生产成本,还提高了产品的市场竞争力,为企业带来了可观的经济效益。
另一家专注于储能电池生产的企业,在电池极耳焊接环节面临着挑战。由于极耳尺寸小、精度要求高,传统焊接工艺难以满足要求,导致焊接不良率较高。引入龙门式振镜激光焊接机后,凭借其高精度的光斑控制和灵活的扫描速度调节能力,实现了极耳的高精度焊接。焊接不良率从原来的 10% 降低到了 2% 以内,有效提高了生产效率和产品质量。同时,设备的操作便捷性也大大减轻了操作人员的工作负担,提高了生产效率。
行业展望与未来趋势
展望未来,新能源锂电池行业将继续保持高速发展的态势,而龙门式振镜激光焊接机作为关键的焊接设备,也将迎来新的发展机遇与挑战。
在技术创新方面,随着激光技术、自动化控制技术以及人工智能技术的不断融合发展,龙门式振镜激光焊接机将朝着更高精度、更高效率、更高智能化的方向迈进。未来,设备可能会搭载更先进的传感器,实现对焊接过程的实时监测和智能反馈控制,根据焊接材料、焊缝形状等参数的变化,自动调整激光功率、焊接速度等关键参数,进一步提高焊接质量的稳定性和一致性。人工智能算法也将被应用于焊接路径规划和缺陷预测,通过对大量焊接数据的分析和学习,优化焊接工艺,提前发现潜在的焊接缺陷,降低废品率。
在应用拓展领域,随着新能源汽车、储能等行业的不断发展,对锂电池的性能和安全性提出了更高要求,这将促使龙门式振镜激光焊接机在新型电池结构和材料的焊接中发挥更大作用。固态电池作为下一代锂电池的重要发展方向,其电极材料和电解质与传统锂电池有很大不同,对焊接工艺提出了全新挑战。龙门式振镜激光焊接机有望通过技术创新,实现对固态电池材料的高质量焊接,推动固态电池的产业化进程。随着锂电池在航空航天、海洋能源等领域的应用逐渐拓展,龙门式振镜激光焊接机也将面临更复杂的焊接工况和更高的技术要求,需要不断优化设备性能,以满足这些特殊领域的需求。
从整个新能源锂电池制造业的角度来看,龙门式振镜激光焊接机的广泛应用将对产业升级和可持续发展产生深远影响。它将助力企业提高生产效率、降低生产成本、提升产品质量,增强我国新能源锂电池产业在全球市场的竞争力。高精度、高质量的焊接工艺能够提高电池的能量密度和循环寿命,减少电池的使用量和废弃物排放,符合绿色发展的理念,为新能源产业的可持续发展提供有力支持。
龙门式振镜激光焊接机作为新能源锂电池焊接领域的核心设备,在当前和未来都将发挥着不可替代的重要作用。相信在技术创新和市场需求的双重驱动下,它将不断突破技术瓶颈,拓展应用领域,为新能源锂电池行业的发展注入新的活力,助力我国在全球新能源产业竞争中抢占先机,实现绿色能源的美好未来。